Installare una pressa piegatrice idraulica MCM Colgar in TubiSteel ha visto ridurre tempi ciclo e costi per manodopera ed energia: il racconto degli aspetti tecnici e funzionali.
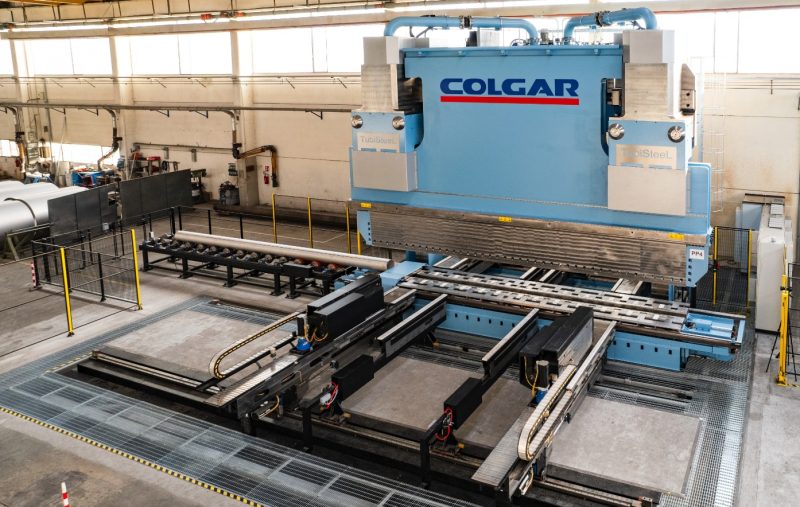
Alta qualità, soluzioni personalizzate e affidabilità hanno sempre caratterizzato gli impianti per la lavorazione della lamiera di Colgar Bending Machines, che dal 1945 realizza presse piegatrici e oggi è una business unit del gruppo MCM – Machining Centers Manufacturing.
Nel tempo la business unit del Gruppo piacentino ha concentrato la propria attività sulla costruzione di macchine a elevata potenza e con alti livelli di automazione. Nella fattispecie, con il brand Colgar viene realizzata una gamma di modelli con potenze di piegatura tra le 1000 e le 5000 t e con configurazioni in singolo e tandem. Tali macchine possono essere vantaggiosamente integrate in complessi impianti di produzione automatica, grazie a software specifici per la gestione completa della movimentazione, dal carico della lamiera all’estrazione del pezzo finito.
Automatizzazione dell’impianto di piegatura
Proprio l’alto livello di automazione e l’affidabilità della stessa sono state le principali leve che hanno portato la TubiSteel di Schio (VI), a dotarsi di una pressa piegatrice idraulica, modello PIS 30062/82, entrata a pieno regime nel settembre 2023.
TubiSteel, già cliente Colgar da oltre 25 anni, produce un’ampia gamma di tubi saldati nei diversi tipi di acciaio inox della serie 300 austenitici, duplex, superduplex, titanio e in tutte le leghe del nichel; tali prodotti trovano principali applicazioni in impianti oil&gas, nelle raffinerie, nelle aziende di estrazione o negli impianti nucleari i quali, a loro volta, forniscono componenti tubolari utilizzati in diversi settori come l’agricolo, il chimico, il farmaceutico, quello della lavorazione della carta e l’energetico.
«La prima esigenza manifestata da Andrea Dani, titolare di TubiSteel – sottolinea l’Area Sales Manager del costruttore piacentino, Marco Antonini – è stata quella dell’automatizzazione dell’impianto di piegatura che avrebbe dovuto consentire a un solo operatore di gestirlo, limitando le sue attività al carico della lamiera e allo scarico della stessa in tempo quasi del tutto mascherato. È facilmente comprensibile l’esigenza della TubiSteel perché, oggigiorno, diventa sempre più critico il problema del reperimento di personale specializzato e quello già presente si avvia alla pensione. Per giustificare questo tipo di investimenti, peraltro, è necessa rio che le macchine lavorino almeno su due turni, se non tre; ne consegue che l’azienda deve potere contare su tre o quattro operatori formati affinché si possa considerare l’investimento in questo tipo di impianti vantaggioso. In tale contesto si comprende, quindi, che l’automazione diventa determinante perché facilita l’utilizzo degli impianti, peraltro sempre più performanti, e riduce il numero di unità di personale a cui affidarne la conduzione. La nostra pressa è stata concepita proprio per raggiungere prioritariamente questo scopo e può essere gestita da un solo operatore. Spintori frontali e posteriori per il caricamento della lamiera, matrice automatica ad apertura variabile e rulliera laterale per lo scarico del tubo finito sono le principali soluzioni tecniche adottate per andare incontro a queste esigenze espresse dalla TubiSteel».
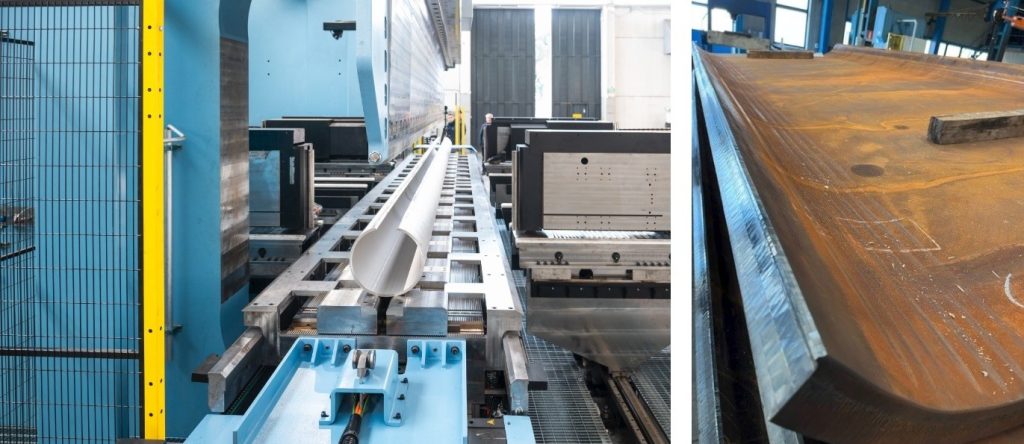
PIS 30062/82, l’high-tech in piegatura
L’impianto presenta dimensioni complessive importanti, con una larghezza di circa 10 m, altrettanti 10 m per l’espulsione laterale del tubo e un’altezza di 7 m, con 5 m che si sviluppano sottoterra. La macchina ha una potenza di 3000 t, con possibilità di concentrare un carico di 1800 t/metro, larghezza utile massima di 8200 mm, libero passaggio tra i montanti pari a 6200 mm, corsa da 800 mm, incavo di 1010 mm e un largo range di piegatura fatto di grandi spessori in relazione alla lunghezza del tubo, il cui diametro massimo realizzabile è di 914 mm. La pressa piegatrice è dotata di spintori frontali e posteriori con guida a terra completi di sistema rotolamento tubo per agevolarne la chiusura, di matrice ad apertura variabile da 0 a 400 mm, con incremento di apertura 20 mm, gestita in automatico dal controllo numerico ESA che è stato personalizzato per la piegatura dei tubi e che raccoglie la pluriennale esperienza dei tecnici di MCM Colgar.
«La rulliera motorizzata per l’evacuazione del manufatto, abbinata all’estrattore motorizzato, è di notevole importanza – evidenzia ancora Antonini – perché permette di liberare l’area di lavoro rapidamente e di consentire all’operatore di caricare la successiva lamiera da piegare, riducendo le tempistiche che ci sarebbero in caso di uscita frontale. Inoltre, un altro punto di forza della nostra pressa è rappresentato dalla possibilità di esecuzione direttamente in macchina dell’invito sulla lamiera piana, ovvero la prima fase di piegatura della lamiera necessaria a fare combaciare i lembi del tubo per la saldatura finale. Si evita così in molti casi di dovere ricorrere alla macchina di preinviti, con evidente aumento dei tempi e dei costi e della movimentazione delle lamiere. Questa funzionalità è resa possibile dall’avere una apertura particolare della matrice; essa permette di eseguire correttamente questa operazione delicata e critica che dipende dalla lunghezza e dallo spessore del tubo da realizzare e che necessita di tutta la potenza per potere essere eseguita in modo corretto».
Non meno importante è la presenza di inverter montati sui motori delle due pompe principali, una per cilindro, che contribuiscono alla riduzione dei consumi energetici principalmente nelle fasi di avviamento, di stand-by e di risalita rapida del pestone. La centrale idraulica, grazie al suo sistema a doppia pompa a portata variabile con controllo della pressione ad alta efficienza, consente un maggiore risparmio energetico rispetto alle soluzioni standard, oltre che una riduzione del rumore e una maggiore durata dei componenti. Il software dedicato alla gestione dell’impianto ha, tra le varie funzionalità, il “Progressive Stand-By” che prevede lo spegnimento pianificato delle unità di potenza in caso di inutilizzo prolungato.
La pressa PIS 30062/82 rispetta tutti i requisiti che sono alla base del concetto di Industria 4.0: è stata completamente interfacciata con il sistema gestionale del cliente ed è completa di teleassistenza per facilitare e velocizzare l’interazione con l’ufficio tecnico di MCM Colgar.
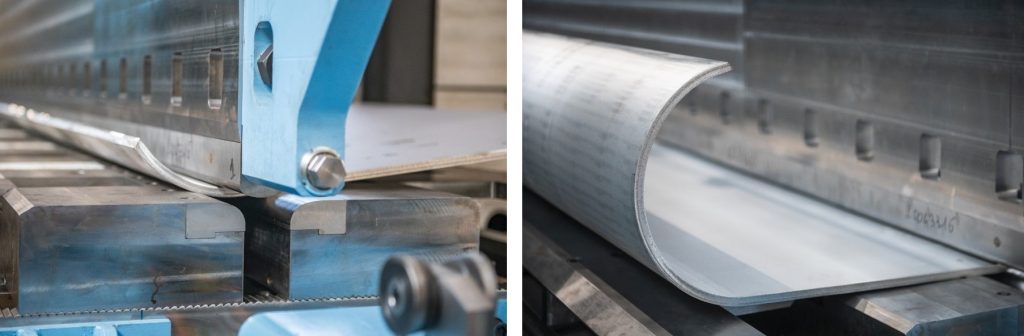
Un investimento lungimirante
«Siamo particolarmente soddisfatti della pressa che abbiamo sviluppato per la TubiSteel – afferma l’Area Sales Manager – perché abbiamo messo a punto una soluzione molto avanzata che ha contribuito significativamente alla competitività del nostro cliente. Basti pensare che normalmente, su altre macchine, un determinato tubo che richiede tempi ciclo di oltre un’ora, sulla PIS 30062/82 vengono più che dimezzati. La nostra pressa è andata ad affiancare quelle già presenti nel sito produttivo dell’azienda vicentina; non è stata dedicata alla realizzazione di una nuova linea di prodotti, bensì è volta a migliorare ulteriormente l’attuale produzione, semplificando ed efficientando i processi aziendali. Tale strategia ha consentito di rispondere in modo sempre più tempestivo alle richieste del mercato, abbattendo ancora di più i tempi di consegna per determinate linee di tubi e mantenendo l’elevato standard di qualità che contraddistingue tutti i prodotti della TubiSteel. Presenteremo questa tipologia di pressa idraulica alla prossima fiera Tube, che si svolgerà dal 15 al 19 aprile 2024 a Düsseldorf in Germania, consapevoli di avere sviluppato una macchina avanzata e molto performante».
a cura di Stefano Belviolandi ed Ernesto Imperio
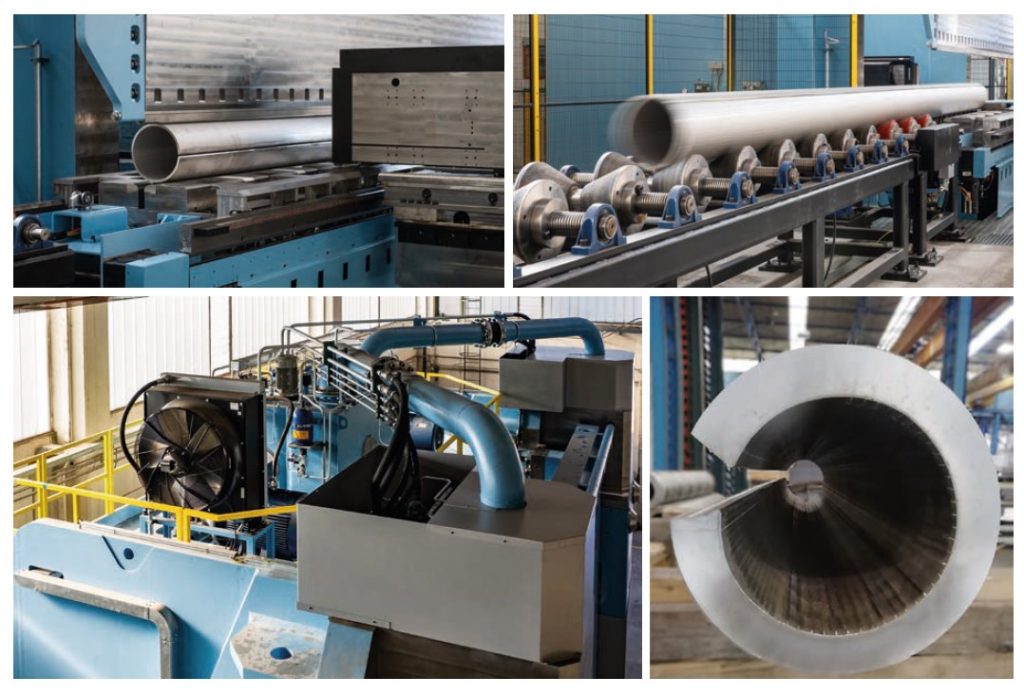
a cura di Redazione
Condividi l'articolo
Scegli su quale Social Network vuoi condividere