Versatilità di utilizzo, affidabilità, precisione e servizio eccellente sono le leve che hanno portato Gilardi ad affidarsi ad AIDA per la fornitura della nuova linea di produzione con servo pressa a doppia riduzione e Sistema ADMS Transfer Simulator, che garantisce l’efficientamento della produttività riducendo i tempi di realizzazione.
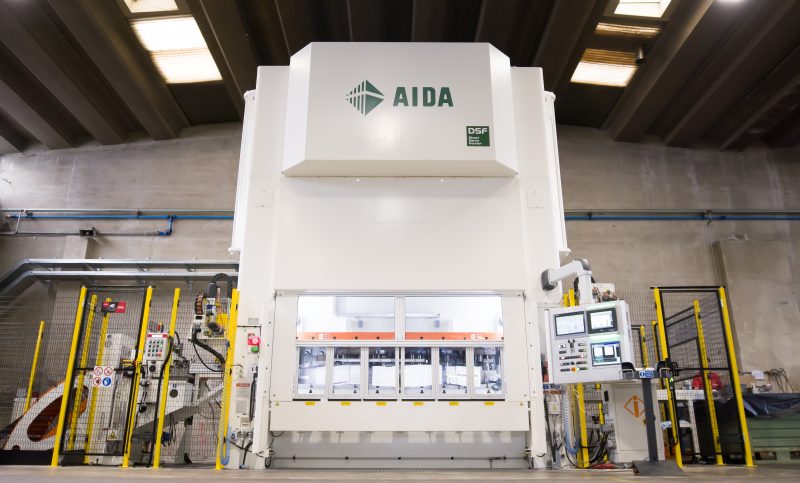
Gilardi, azienda con sede a Olginate in provincia di Lecco, specializzata nella progettazione e costruzione di stampi e stampaggio lamiera a freddo, si è rivolta ad AIDA, realtà di riferimento nella realizzazione di soluzioni di qualità per lo stampaggio e la deformazione dei materiali, per ottenere il massimo efficientamento produttivo e rispondere alle differenti e mutevoli richieste del mercato.
Linea con servo pressa AIDA per efficientare la produttività
Nell’ottica di garantire la massima flessibilità nei confronti del mercato e del cliente effettuando lavorazioni per un’ampia gamma di tipologie di pezzi, dai più piccoli da 10-15 grammi ai più voluminosi, dove i tonnellaggi per sforzo e per complessità dell’attrezzatura sono più importanti, Gilardi dispone di un completo parco macchine costantemente aggiornato. Al fine di ottenere prodotti di dimensioni e complessità sempre maggiori, incrementando con sguardo rivolto al futuro la capacità produttiva, nel 2023 è stata installata una nuova linea tecnologica di stampaggio composta dalla servo pressa AIDA DSF-M2-6300(2)-305-150 equipaggiata con transfer gestito da PLC AIDA e completata dalla linea di alimentazione lamiera Saronni.
Pressa a doppia riduzione con alto rating point
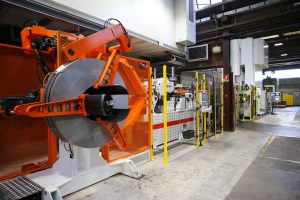
La pressa a doppia riduzione con alto rating point per la gestione di spessori elevati è stata realizzata interamente negli stabilimenti AIDA per garantire il più scrupoloso controllo in tutte le fasi di costruzione, così come il rispetto dei tempi di consegna. Rappresenta lo stato dell’arte per quanto riguarda le caratteristiche tecniche: le guide della slitta sono a pattini e a rulli a secco, al fine di assicurare un maggiore controllo e la massima pulizia. Particolare attenzione è stata riservata da AIDA, inoltre, alla sostenibilità ambientale e al risparmio energetico mediante l’utilizzo di motori raffreddati ad aria. La parte elettrica, in alternativa ai tradizionali quadri che venivano posizionati sul soppalco, è stata realizzata in un apposito container climatizzato nel quale sono racchiusi tutti i componenti, consentendo una veloce installazione e successivamente garantendo la massima accessibilità da parte dell’operatore e facilità di manutenzione.
Sistema ADMS Transfer Simulator di AIDA
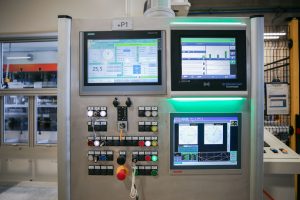
Il sistema ADMS Transfer Simulator di AIDA incluso nella fornitura permette, tramite un’elaborazione software, di ottimizzare il ciclo del transfer combinandolo con il movimento pressa. I principali vantaggi sono rappresentati dalle tempistiche ridotte per la messa in produzione di uno stampo transfer, in quanto la programmazione avviene in modo semiautomatico dal software e anche offline in ufficio tecnico prima che a bordo macchina, dove successivamente viene effettuata solo l’ottimizzazione del ciclo. Il software, secondo gli ingombri e le dimensioni che vengono imputati in fase di programmazione, definisce la migliore combinazione dei movimenti pressa e transfer e offre già una simulazione della velocità massima ottenibile. Tutto ciò facilita notevolmente l’attività dell’operatore, in quanto gran parte delle scelte vengono effettuate dal software sulla base dei dati dimensionali dello stampo che vengono forniti dall’ufficio tecnico. In aggiunta è possibile simulare offline la cadenza futura e ipotetica dello stampo. Questo consente, in fase di preventivazione e chiusura del progetto, di apportare eventuali migliorie per aumentare la produttività qualora ci fosse qualche ingombro o aspetto che possa limitare il funzionamento del transfer.
Linea di produzione ideale per gestire alti spessori
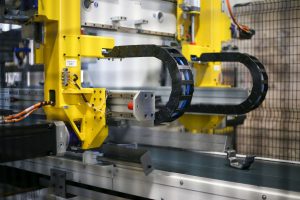
L’impianto è completato da una linea di alimentazione notevolmente flessibile. In collaborazione con Saronni è stata sviluppata una linea che permettesse di avere una gamma di spessori lavorabili molto ampia, da 0,8–1 millimetro fino ad arrivare a 9 millimetri, così come un’elevata velocità nelle operazioni non produttive. Il cambio del nastro, per esempio, avviene in modo completamente automatico; è presente un doppio svolgitore che alla fine del precedente posiziona quello successivo mentre un’unità di saldatura unisce i due coil, permettendo un’operazione veloce che evita tempistiche di fermo macchina e permette un migliore utilizzo del materiale, riducendo gli scarti. Anche per quanto riguarda il cambio attrezzatura tutte le regolazioni, tra cui larghezze e posizione della testa di raddrizzatura, avvengono in modo automatico: l’operatore riceve dal sistema gestionale l’ordine di produzione che viene impostato e tutti i parametri si configurano in funzione del nastro che sarà introdotto.
Gilardi: una realtà in espansione
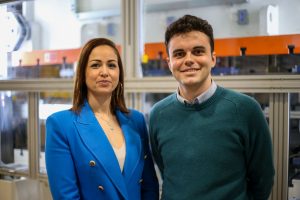
Fondata nel 1970 dai fratelli Gilardi l’azienda ha iniziato la propria attività nel settore del mobile, specializzandosi nella produzione di guide per cassetti e particolari attinenti a questo comparto, diversificando successivamente il business grazie all’esperienza maturata, unitamente alla possibilità di realizzare al proprio interno gli stampi. Sotto la guida dei figli dei fondatori – Eleonora Gilardi, Sales & Marketing Manager, e Marco Gilardi, Operations Manager – l’azienda impiega attualmente 50 addetti ed è attiva nel settore automotive, che copre circa il 60% della produzione, affiancato da industria del bianco e comparto elettrico, oltre a due linee a marchio Gilardi attinenti l’ambito idrosanitario e del mobile. Il 50% della produzione è rivolta al mercato italiano mentre l’altra metà è destinata all’estero e in particolare Germania, Francia e Polonia. A fronte del trend intrapreso in costante aumento, per i prossimi anni le prospettive di crescita riguardano in particolare i mercati europei.
Ė possibile leggere la versione completa dell’articolo qui: https://viewer.joomag.com/tecnolamiera-apr-mag-2024/0285981001713371350
di Davide Davò, Maria Bonaria Mereu e Andrea Baruffi
a cura di Maria Bonaria Mereu
Condividi l'articolo
Scegli su quale Social Network vuoi condividere